What Are 1/4 and 1/8 Aluminum Sheets So Popular
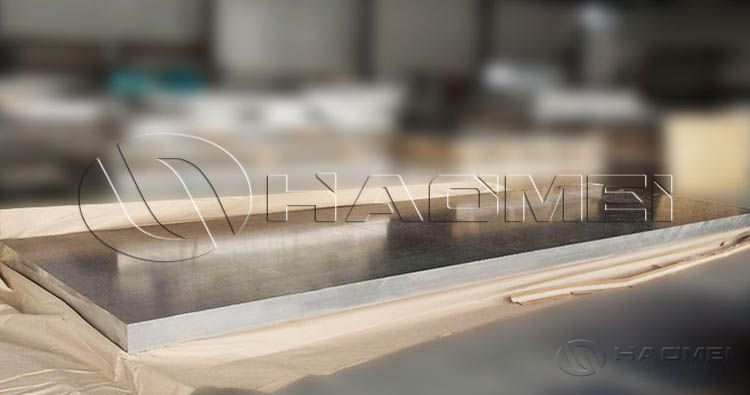
Aluminum sheet is one of the most commonly used metal materials in modern industry. Its thickness selection directly affects product performance, processing efficiency and cost control. 1/4 inch and 1/8 inch aluminum sheet accounts for more than 65% of th
Aluminum sheet is one of the most commonly used metal materials in modern industry. Its thickness selection directly affects product performance, processing efficiency and cost control. 1/4 inch and 1/8 inch aluminum sheet accounts for more than 65% of the global aluminum sheet consumption. Why are they so popular?
1/4 inch (6.35mm) aluminum sheet: King of structures
1 4 aluminum plate is suitable for building curtain wall supports, automobile chassis reinforcement beams and pressure vessel heads.
Core advantages:
Single-point static load can reach 120MPa, meeting the needs of heavy-duty structures
It Can withstand high temperature environments above 300℃ without losing strength
Suitable for high-precision connection processes such as TIG welding.
1/8 inch (3.175mm)aluminum sheet: All-rounder
The typical applications of 1 8 aluminum sheet are electronic equipment housing, aviation interior parts, decorative panels,etc.
Outstanding features:
Density is only 1/3 of steel, with significant weight reduction effect
Elongation can reach 25%, suitable for complex curved surface forming
Unit cost is 20%-30% lower than 1/4 inch plate.
Industrial code for thickness control
Modern aluminum plate production has achieved a thickness accuracy of ±0.01mm. Key technologies include:
1. Rolling process optimization
Hot rolling stage: Dynamically adjust the rolling force through the hydraulic AGC system to control the plate thickness fluctuation within ±0.1mm
Cold rolling process: Use a six-roll CVC rolling mill with an emulsion cooling system to achieve micron-level thickness uniformity
2. Heat treatment coordination
Annealing process: Keep warm at 400-450℃ for 2 hours to eliminate cold rolling stress and stabilize the grain size
Online quenching: Use a water mist cooling system to control the temperature difference in the thickness direction of the plate within ±5℃
3. Detection technology innovation
Laser thickness gauge: Real-time scanning accuracy of ±0.005mm, collecting 1000 data points per second
Ultrasonic flaw detection: Can detect areas with thickness deviation exceeding 0.02mm and automatically mark them.
Typical applications
New energy vehicle battery tray
Using 1.5-3mm thick aluminum plate, it is formed in one piece through die forging process, which not only ensures the protection strength of the battery pack, but also reduces the weight by 35%.
5G base station radiator
0.8mm thick aluminum foil is combined with 3mm thick substrate, and the heat dissipation efficiency is increased by 40% through microchannel design.
Aerospace structural parts
4-6mm thick high-strength aluminum alloy is selected. After CNC milling, it reduces material consumption by 15% while ensuring the safety factor.
Golden rule for thickness selection
Function priority: 1/4 inch is preferred for load-bearing structure, and 1 8 aluminum sheet is selected for lightweight requirements.
Process adaptation: thin aluminum sheet is selected for complex forming, and thick plate is selected for welding structure.
Cost consideration: For every 1mm increase in thickness, the material cost increases by about 12%.
Future trend: With the improvement of aluminum alloy strength, the application proportion of 0.5-2mm thin plate is increasing at an annual rate of 8%.
Inquiry
TABLE OF Contents

Haomei Aluminum CO., LTD.
Tel/Whatsapp: +86-15978414719
Email: sale@alumhm.com
Website: https://www.alumhm.com
Xin'an Industrial Assemble Region,Luoyang,Henan Province,China
Office Add: 1103, No.14 Waihuan Road, CBD, Zhengzhou, China